Introduction of Chuck Hull:
In today’s life, the printer became the most important part of everyday life. He is the inventor of the solid imaging process known as stereo lithography, which is called 3D printing; he made the first commercial prototype technology and the STL file format. Chuck Hull inducted into the National Inventions Hall of Fame in the year 2014. Let’s talk about the history of the inventor and also the history of printers.
Basic Information | Chuck Hull |
Nationality | United States of America |
Date of Birth | 12th May 1939 |
Place of Birth | The University of Colorado, United States of America |
Date of Death | Alive |
Place of Death | Alive |
Age | 81 years old |
School | Central High School |
High School / College | Central High School |
University | The University of Colorado (1961) |
Occupation | Engineer in Physics field |
Career | 1983–present |
Famous for | The inventor of the 3D printer |
Other works | 3D Systems in Valencia, California |
Awards | European Inventor Award.Industrial Research Institute’s IRI Achievement Award |
Early life and education:
Early life:
Throw Hull (Charles W. Structure; born on 12th May 1939) is the prime supporter, leader VP, and boss innovation official of 3D Systems. He is one innovator of the SLA 3D printer, the major business quick prototyping innovation, and the broadly used STL record design.
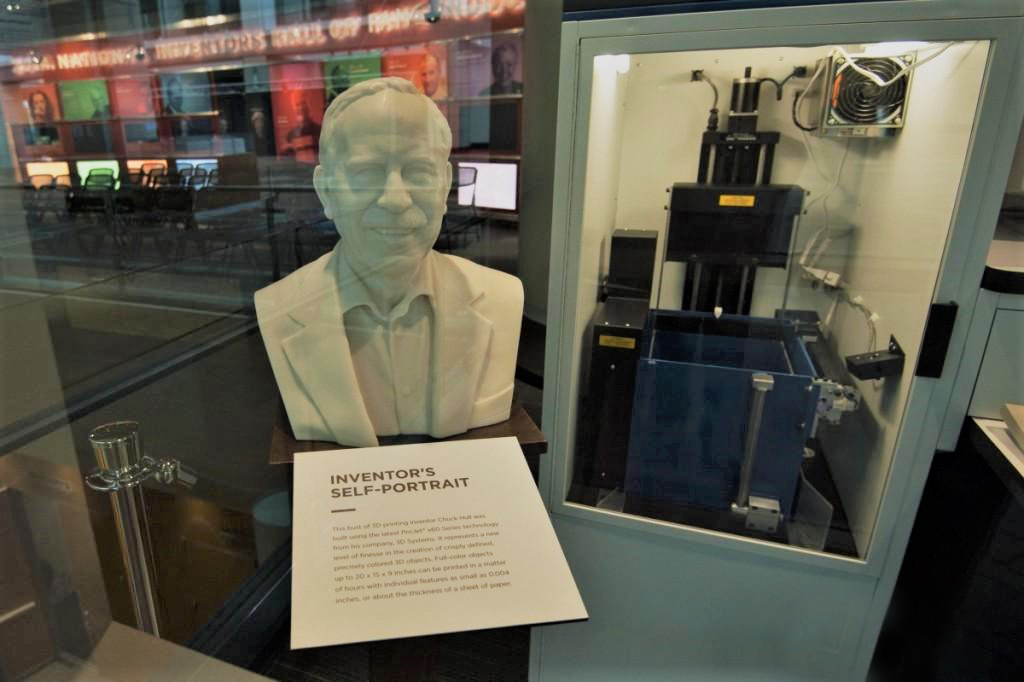
Chuck Hull named on over 60 U.S. licenses just as different licenses the world over in the fields of particle optics and quick prototyping. He enlisted into the National Inventors Hall of Fame in 2014, and 2017 was one of the initial inductees into the TCT Hall of Fame.
Toss Hull conceived on 12th May 1939, in Clifton, Colorado, the child of Lester and Esther Hull. His initial life spent in Clifton and Gateway, Colorado. He moved on from Central High School injunction, Colorado. Toss got a BS in designing material science from the University of Colorado in 1961.
Ultraviolet Lights in 1984:
Frame previously thought of the thought in 1983 when he was using UV light to solidify tabletop coatings. But on July 16, 1984, Alain Le Méhauté, Olivier de Witte, and Jean Claude André documented their patent for the stereo lithography process. It was three weeks before Chuck Hull recorded his patent for stereo lithography. Using French designers surrendered by the French General Electric Company (presently Alcatel-Alsthom) and CILAS (The Laser Consortium).
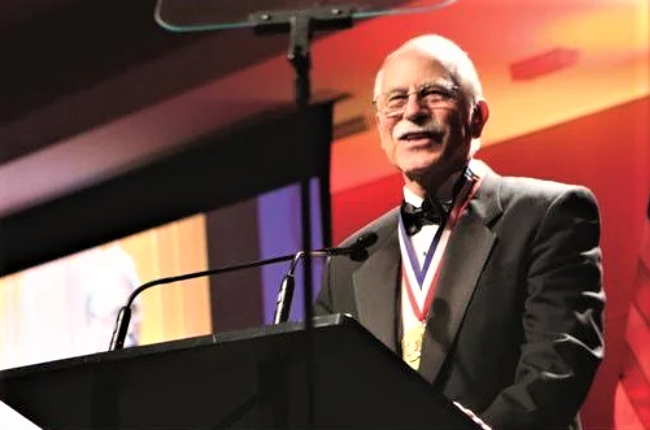
The guaranteed reason was “for the absence of business viewpoint”. Structure authored the expression “stereo lithography” in his U.S. Patent 4,575,330 named “Mechanical assembly for Production of Three-Dimensional Objects by Stereo lithography” gave on 11th March 1986. He characterized stereo lithography as a technique and device for making powerful items by progressively “printing” meager layers of the bright reparable material, one on top of the other. In Hull’s patent, a concentrated light emission light is engaged onto the outside of a tank loaded up with fluid photopolymer[1].
Beginnings of Stereo Lithography:
The light pillar, moving under PC control, draws each layer of the item onto the outside of the fluid. Any place the bar strikes the surface, the photopolymer polymerizes/cross links and changes to a strong. A serious CAD/CAM/CAE programming numerically cuts the PC model of the item into an enormous number of slender layers. The cycle at that point constructs the item layer by layer beginning with the base layer, on a lift that is brought down somewhat after hardening of each layer[1].
Business Prototyping:
In 1986, Chuck Hull began business fast prototyping when he established 3D Systems in Valencia, California. Hull understood that his idea not restricted to fluids and hence gave it the conventional name “stereo lithography” (3D printing), and recorded wide patent cases covering any “material fit for cementing” or “material equipped for adjusting its actual state.”
The body developed a patent portfolio covering many basic parts of the present added substance producing innovations, for example, information planning using located models (STL record configuration) and cutting, and presentation techniques, for example, exchanging hatch headings. The reward for his function as 3D Systems CTO was $307,500 in 2011[1].
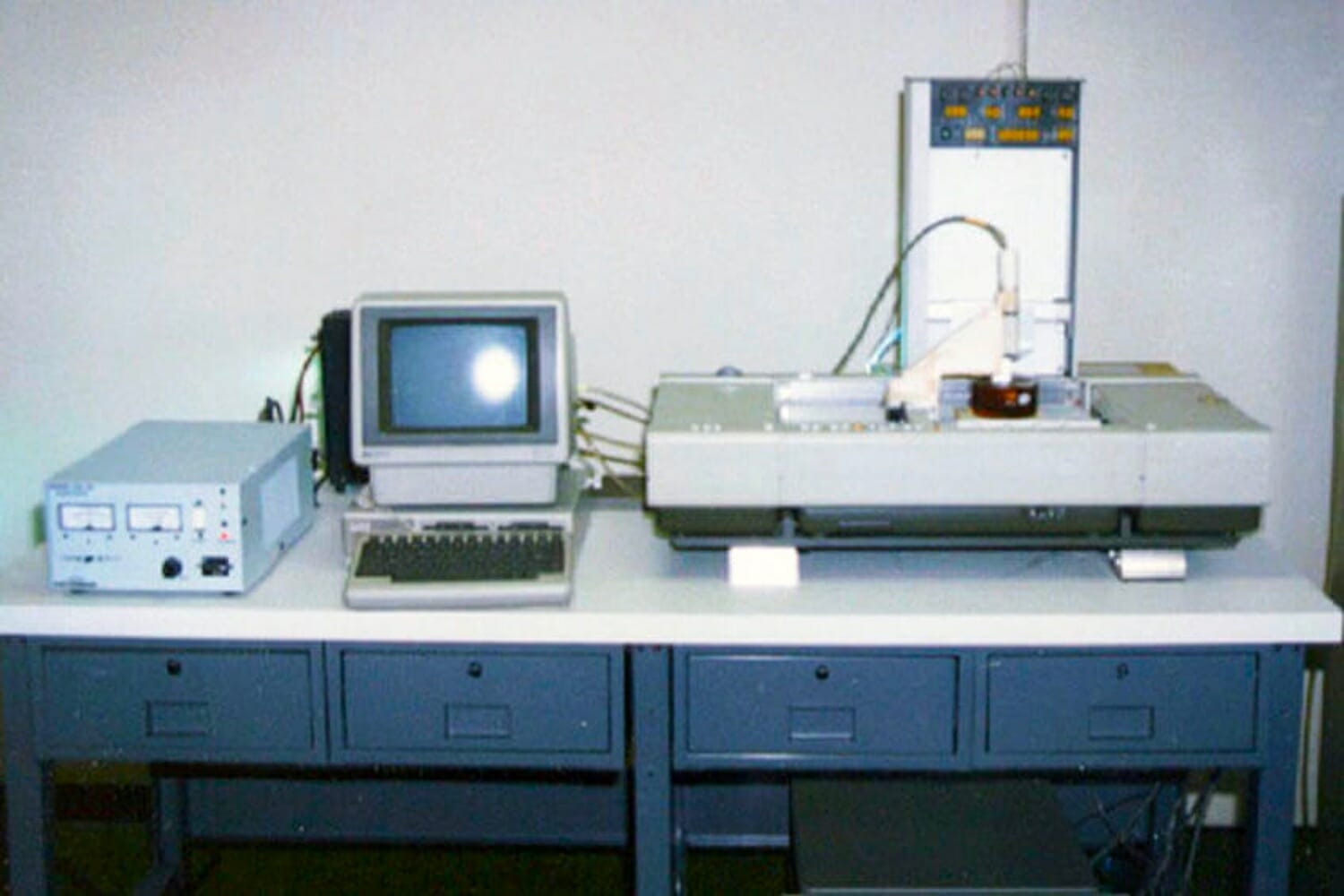
Improvement of SLA and 3D Systems:
SLA is a cycle of building 3D structures from an automated plan. Many meager layers of a fluid UV-reparable photopolymer gum relieved, one on top of another, using a UV laser to follow and cement an example and making each layer stick to the layer underneath. SLA incredibly decreased the time it takes for planners and specialists to make an ideal plan or practical 3D model.
In the wake of licensing the 3D producing measure in 1986, Hull established 3D Systems, which popularized the principal quick prototyping framework for PC helped plan programming. The organization is presently the major supplier of business and family 3D printers and plan efficiency instruments for computerized production [1].
The Latest Advancement in the 3D Printers:
3D Systems’ latest advancement is a $1,300 Cube printer that makes plastic 3D articles, for example, toys and gems, and advertised to purchasers, leisure activity originators, and carport business people. Structure considers this most recent headway a “democratization” of admittance to 3D printing.
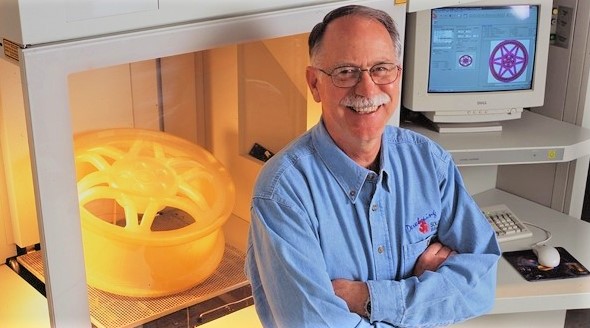
3D Systems has been very effective, announcing incomes of $90.5 million in the second from last quarter of 2012, a 57% expansion over a similar period in 2011. It declared in October 2012 that it expects about $350 million in income before the finish of 2012.
The structure has a BS in designing material science from the University of Colorado (USA) and a privileged doctorate in designing from Loughborough University (UK). He was attempting to create UV-reparable tars for Ultra Violet Products in California when he made the achievement [1].
Study Related to the Stereo Lithography:
SPIE Professional as of late talked with Hull about the business and study of stereo lithography and 3D printing. In the mid-1980s, I contemplated whether photopolymer science could imaged to rapid make first-article (model) plastic parts since it took six to about two months to get first-article parts from the customary instrument making and trim cycles. And afterward, the plan typically had issues, and it must have done over. Planning in plastic was a very tedious and costly cycle.
Stereolithography made extraordinary interest since it tackled the primary article issue; it was a fast prototyping framework. Considering that, the organization developed quickly, extended Stereo lithography frameworks, and created cheaper ink-fly based 3D printers [1].
3D Printers in Different Organizations:
Many contending organizations and advances arose, each with their way to deal with 3D printing. Throughout the long term, 3D Systems kept on growing new sorts of printers, and the organization gained a few different organizations and innovations in the field. Clients of 3D printing have been extremely inventive in many many fields, which has prompted development and variety in the field. This entire has prompted what 3D printing is today. Cellphone covers, shoes, and different articles can printed with 3D Systems’ Cube 3D printer [1].
Photograph Courtesy 3D Systems:
The innovation required dominating photochemistry, laser optics, optical filtering, accuracy mechanical instruments, machine-control programming, 3D picture control programming, measure designing, and framework mix. I made the first stereo lithography framework with no one else in a lab that my boss let me use. This was exceptionally essential; however, it showed the idea. Considering that, we framed the new organization, 3D Systems, and got all the unique ability to create business frameworks.
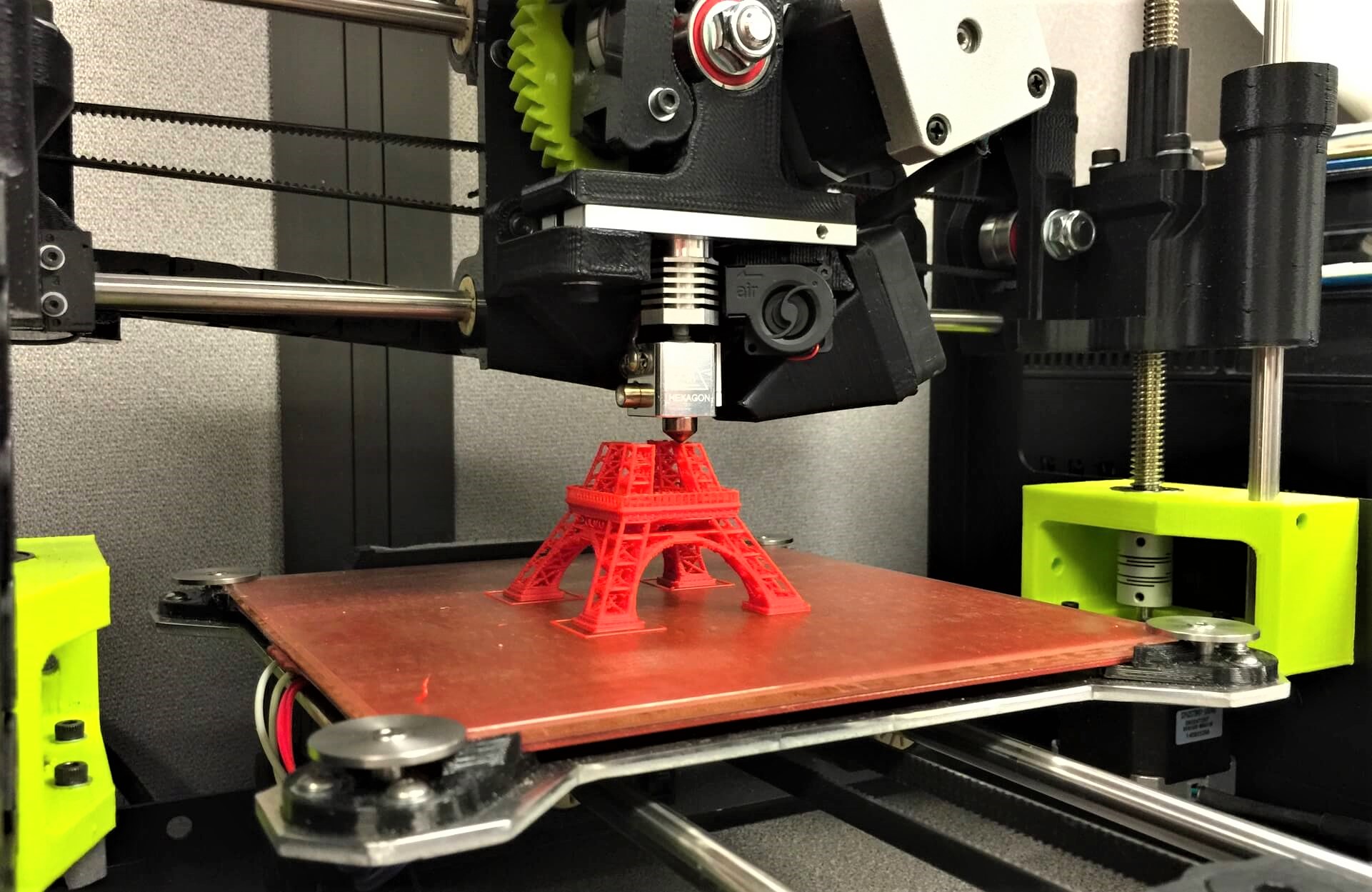
We had enormous premium from the earliest starting point, and our spearheading clients contributed directly close by us to learn and help develop the innovation to where it is today. We feel favored to have worked with so many incredible trailblazers and we keep on joining forces intimately with our clients today.
The first was getting a venture to push the item ahead. At that point, there is consistently the test of a convincing and manageable plan of action. All was good and well to convey a reasonable 3D printer for the general population. That and taking a shot at extraordinary 3D content for anybody and everybody to exploit are the principal challenges we find in offering a convincing shopper prologue to 3D printing [1].
Frameworks Using SLA and Particular Laser Sintering:
Creation frameworks using SLA and particular laser sintering (SLS) request a premium in the market since we keep on advancing their abilities to suit our clients’ prerequisites. The genuine cost advancement has been in section level frameworks — conveying incredible incentive for the expense — and in our capacity to convey expanding levels of usefulness from our long periods of involvement with the outstanding quality to the expert 3D-printer market.
I would state that 3D Systems is striving to democratize admittance to 3D printing by situating the correct innovation at an entirely moderate cost over our developing base of clients and shoppers.
We will place innovative apparatuses under the control of everybody–without respect for their specialized capacities. Set forth plainly, we see a future when everybody can make a lot in 3D with genuine shading book effortlessness. In the previous 25 years, a couple hundred thousand individuals have had the option to plan with the complete opportunity of creation. Simply envision what happens when billions of us get entrance? Advancement and inventiveness will far outperform anything we know today.
The absolute first cup that was printed is one of my unsurpassed top choices. My better half keeps it with her still today, and we will commend the 30th commemoration for that part one year from now. I will reveal to you I likewise got the absolute first business Cube–and promptly printed a neon green iPhone cover. While there are many stunning things we have printed, when I recall over right around thirty years, maybe the clinical model that specialists used in 2003 to effectively isolated the Egyptian twins joined at the head will consistently stay one of the key items to me [1].
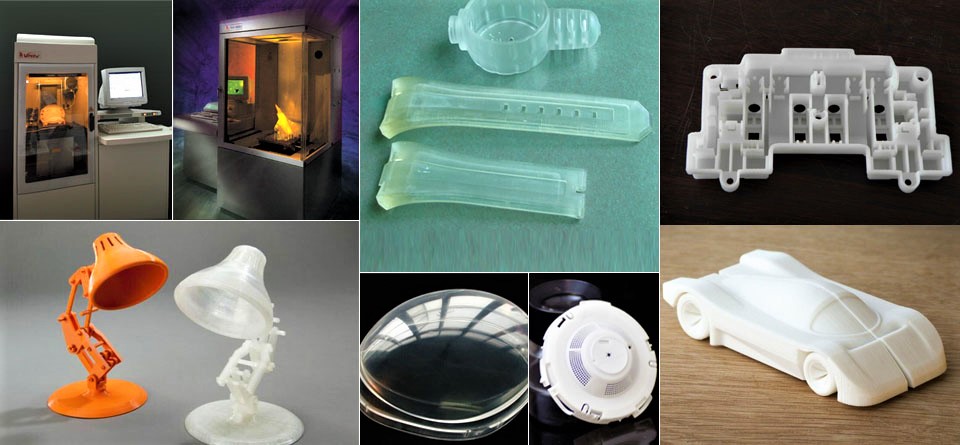
Laser-based Added Substance Fabricating Spreads:
The U.K. also, U.S. governments are among many countries subsidizing projects to quicken the turn of events and commercialization of laser-based added substance producing advances.
The U.K. Innovation Strategy Board will contribute £7 million on 3D printing advancements with its “Rousing New Design Freedoms in Additive Manufacturing” rivalry. United States in 2012 dispatched a pilot establishment to fill in as a proof-of-idea for its National Network of Manufacturing Innovation. The pilot foundation is in Ohio and will center on added substance producing advances, for example, 3D printing.
Lawrence Livermore National Laboratory (USA) is arranging a significant push in its exploration programs gave to add substance producing advancements like stereo lithography. At its Center for Micro and Nano Technology in California (USA), LLNL creates applications for the Departments of Energy, Defense, and Homeland Security. The lab will team up with U.S. producers to create effective advances for their assembling measures [1].
History of 3D Printing:
Some work area 3D printers are modest these days — and they can fit on your work area or in a microwave-sized corner in your kitchen. This wasn’t the situation. For much of the historical backdrop of 3D printing, these machines were the size of little tents, cost a huge number of dollars, and were fit distinctly for specialty ventures.
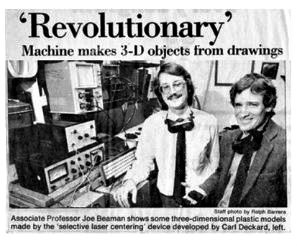
You might amazed to realize that regardless of its appearance as another imaginative innovation, 3D printing has been around since the mid-1980s. What used to be simply mechanical 3D printers the size of little cranes changed into conceivably the answer for organ deficiencies, the lodging emergency, and the democratization of assembling, in only 30 years.
The historical backdrop of 3D printing is a long story, and we felt it was critical to incorporate everything applicable to the most recent 30 years of progress. We split the historical backdrop of 3D printing into four primary parts [2]:
- i. History of 3D printing Part 1–Inception: 1980–1995.
- ii. History of 3D printing Part 2–Adolescence: 1996–2009.
- iii. History of 3D printing Part 3–Young Adulthood: 2009–2014.
- iv. History of 3D printing Part 4–Cusp of Maturity: 2015–the present day.
1984–87: Early History of 3D printing and innovation of Stereolithography:
After three years in 1984, three French specialists named Alain Le Méhauté, Olivier de Witte, and Jean Claude André recorded a patent for the Stereolithography cycle. They were to pioneer another assembling cycle that was to reform fabricating!
However, it wasn’t to be. The three men relinquished the patent not long after they documented it, referring to ‘absence of a business point of view.’ looking back, I’m certain they’re gutted.
Only three weeks after the French architects, Charles ‘Toss’ Hull recorded his patent for Stereo lithography, with new highlights, for example, the STL document design and advanced cutting. His cycle used bright light to fix photopolymers. Since documenting and gaining the licenses by 1986, Chuck Hull framed 3D Systems and delivered the principal ever 3D printer, the SLA-1, in 1987. 3D printing conceived [2].
History of 3d Printing Throw Body SLA-1 3d Printer:
It is in this manner doubtful that either Chuck Hull or Dr. Kodama concocted 3D printing, however, Chuck Hull credited unquestionably more and as it should be. Thoughts are simple, executing them is the critical step [2].
1988–92: Stratasys, EOS, and FDM and SLS to equal SLA:
Stereolithography had a rivalry in the 3D printing space, with rival measures being developed. In 1988, Carl Deckard at the University of Texas recorded a patent for Selective Laser Sintering (SLS) innovation. Rather than utilizing UV light, SLS used a laser to follow and harden layers of powder polymers. This imaginative innovation then rented to DTM Inc to use.
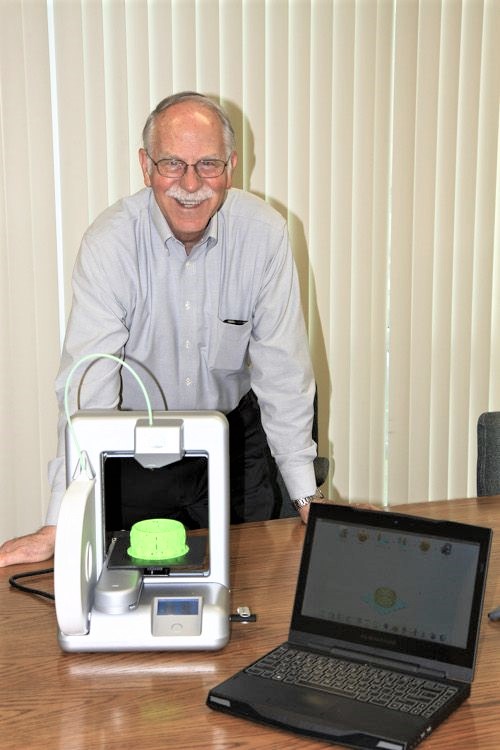
At that point, it turned into a three-horse race. Scott Crump helped to establish Stratasys in 1989 and documented the patent for Fused Deposition Modeling, likely the most notable 3D printing innovation today. 3D Systems and Chuck Hull may have had a head start, yet contenders were hot behind him.
This opposition additionally exacerbated by the establishing of EOS in 1989 in Germany by Dr. Hans Langer. The German juggernaut would overwhelm the SLS 3D printer market, just as pioneer Direct Metal Laser Sintering during the 90s.
After the SLA-1 a couple of years earlier, Stratasys delivered their first FDM 3D printer in 1991. This was the main genuine rivalry for 3D Systems, as each had the patent rights to two different 3D printing advances. FDM parts were more grounded and all the more artificially safe, yet SLA parts could make snappier, and all the more precisely [2].
1993–95: ZCorp, Color Jet 3D printing, and development:
Even though less known in the present day, ZCorp was another significant 3D printing organization back in the mid-90s. In 1993, MIT built up a 3D printing strategy dependent on inkjet printers–the ones we used to print in our workplaces on paper [2].
1996–98, The Excursion to Democratization:
The initial ten years of the historical backdrop of 3D printing prompted the introduction of future goliaths, for example, 3D Systems, Stratasys, and EOS. During the 1990s, they were relative minnows contrasted with the billion-dollar valuations they currently have [2].
The last part of the 1990s was another significant time for recently settled 3D printing organizations. 1997 saw the production of Arcam, who represents considerable authority in metal 3D printer machines and who are the main maker of Electron Beam Melting (EBM) 3D printers [2].
1999–2002: printed bladders and Envision TEC”:
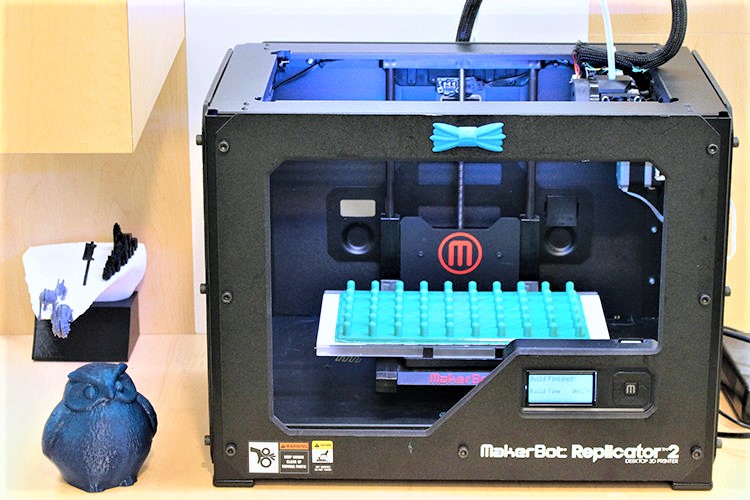
The turn of the thousand years brought another arrangement of achievements for 3D printing. ZCorp uncovered the first multicolor 3D printer, while Objet Geometries delivered their first inkjet 3D printer, both in 2000. Even though Stratasys and 3D Systems were as yet two of the greatest names in the business, producing an assortment of modern machines, these persevering understudies were filling in size and height [2].
The 3D printed bladder was only the beginning for bio printing and 3D printing’s progressing convenience in clinical medicines. In 2002, a 3D printed scaled-down human kidney made, again at the Wake Forest Institute for Regenerative Medicine [2].
2004–05: Beginnings of RepRap and 3D Printing goes HD:
During the years 2004 and 2005, the beginnings of what is seemingly the absolute most significant occasion in 3D printing history happened. 3D printing had propelled a senior teacher at the University of Bath, Dr. Adrian Bowyer, and had thoughts for 3D printers that could self-reproduce assembling more forms of themselves [2].
2005–08: Binder Jetting, RepRap gets suitable:
In 2005, ExOne set up as an independent organization from the Extrude Hone Corporation. ExOne would turn into an innovator in Binder Jetting 3D printing, equipped for 3D printing objects in metal just as sandstone. Folio Jetting can make full-shading sandstone objects, just as metal parts with complex calculations [2].
Albeit now known, a little site called Thingiverse, possessed by a youngster organization called MakerBot dispatched in 2008. Thingiverse permitted fashioners to transfer their 3D printer models based on different 3D programming for others to download for nothing and print at home [2].
2009–2014: The principal moderate FDM 3D printers:
A patent ended between the end last part of 2008 and the start of 2009. The serious deal, licenses lapse constantly right? This patent possessed by a now enormous organization called Stratasys, for Fused Deposition Modeling innovation.
FDM is the most straightforward 3D printing innovation; it includes warming up a plastic fiber until it melts and afterward expels it out layer-by-layer [2].
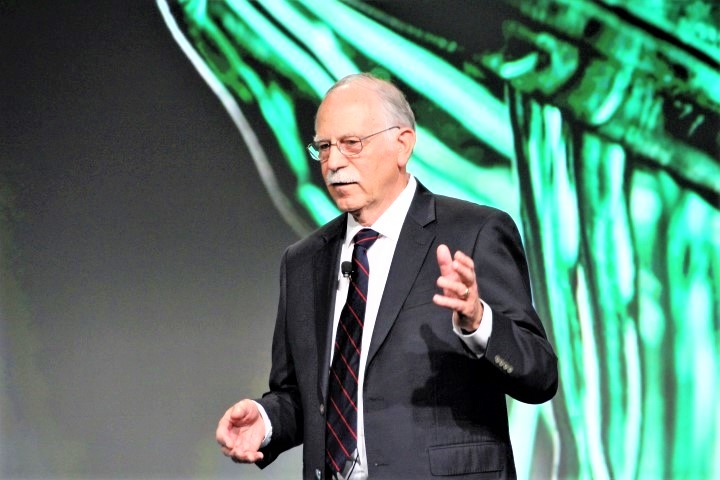
The principal moderate FDM 3D printer unit delivered in January 2009. It known as the BfB RapMan printer, and even though it was first; it wasn’t appalling. Future emphases made, and maybe it would have had a greater effect if the youngster organization we referenced before hadn’t seemed three months after the fact [2].
Lately, online 3D printing administration organizations had jumped up to gain by the developing interest for 3D printed parts. These administrations work by permitting clients to transfer models they have either planned or downloaded and pay for them to 3D printed and sent to their entryway. Some even permit clients to sell their plans on an online commercial center and get paid for their plans [2].
2012–14: The democratization of Stereolithography:
Although the first licenses for Stereolithography had ended over five years prior, no one had at this point had the option to make a reasonable SLA 3D printer. This changed in June 2012 when the B9Creator delivered in the wake of raising over $500,000 on Kickstarter. The B9Creator used a comparative innovation to Stereolithography called Digital Light Processing (DLP), and could pre-requested for $2,375 [2].
2012–13: Stratasys and Objet blend, Stratasys purchases MakerBot:
Objet Geometries had gone from solidarity to quality since the mid-2000s, improving their PolyJet innovation that could print in full-shading. This in the end prompted potentially the greatest securing throughout the entire existence of the 3D printing industry. On 16th April 2012, Stratasys declared it had converged with Objet in an all-stock exchange, with Stratasys being the enduring organization [2].
Cody Wilson and the 3D printed firearm:
Later in 2013, Cody Wilson turned into a viral sensation after his organization Defense Distributed posted an STL record on its site for 3D printing a working 3D printed firearm. The US Government requested Defense Distributed to eliminate the plans three days after the fact, yet the weapon had just downloaded over 100,000 times [2].
2014: 3D Printing in space, and SLS and SLA licenses lapse:
The next year, a healthier accomplishment in 3D printing figured it out. NASA reported they had used a 3D printer in space and made the main 3D printed object in space in 2014. This opened the entryway for future space production and the capacity of future space travelers to provoke instruments on-interest in space. On the off chance that the group in space required a specific thing, they could ‘radiate’ the plan from Earth at light speed, and 3D print the instrument out in space [2].
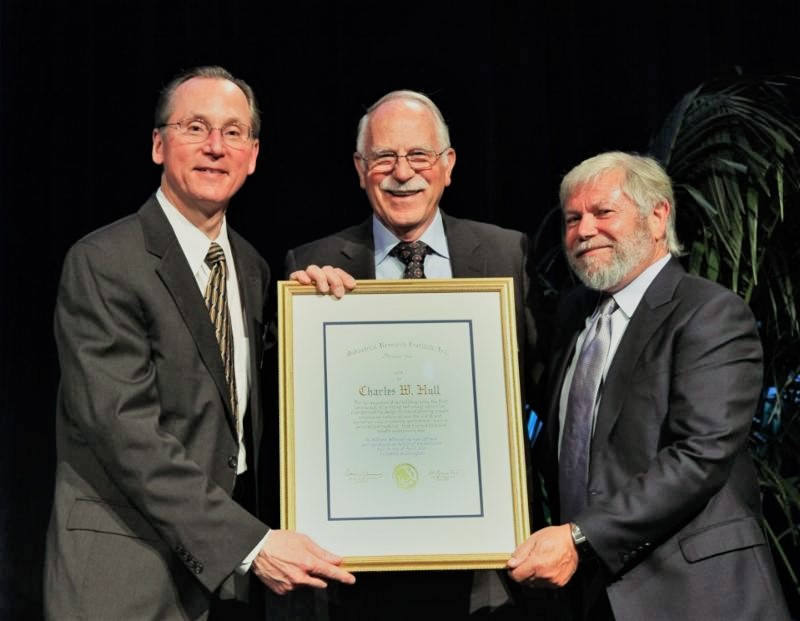
Carbon 3D and Desktop Metal: 0 to $1 billion every 3 years:
Carbon 3D was framed on 11th July 2014 in California by Joseph and Philip DeSimone. The primary tech behind the organization enlivened by Terminator 2 and named CLIP (Continuous Liquid Interface Production). Before the finish of 2017, the organization had raised over $360 million and had a valuation of $1.7 billion—more than Stratasys and 3D Systems (the two organizations fell forcefully in esteem after the 2013-14 3D printing craziness faded away from valuations in an abundance of $3 billion beforehand) [2].
References:
1. 21st November 2020; Available from: wikipedia
2. 21st November 2020; Available from: 3dsourced